Below is the common information required to help cross or specify an appropriate VFD.
#1 Are there any size constraints regarding the physical size the new drive? If so, what are the maximum Height X Width X Depth dimensions in inches (or millimeters) required of the drive to fit into the mounting location?
#2 What is the required enclosure rating of the drive? This relates to the Drives environment.
Most common ratings:
- IP20 – Typically mounted in a protected climate controlled enclosure. Finger safe but susceptible to dust and moisture.
- NEMA 1 / Type 1 – Can be mounted in an enclosure, or on a wall in a clean (no dust, no water) environment. NEMA 1 drives typically have knockout holes to land conduit fitting or strain reliefs.
- IP55 – Protection against dust and low pressure jetting water. Good for dusty environments with minimal to no moisture.
- IP66 / NEMA 4X – Protection against high pressure jetting water, corrosive agents (i.e food processing plant wash down requirements), outdoor application.
#3 What is the application (Heavy Duty/Constant torque vs. Light Duty/Variable torque)?
Examples:
- Heavy Duty: Conveyor, Extruder, Mixer, Rock crusher, crane, Fixed displacement pump. Anything with a potentially high starting load.
- Light Duty: Fan, variable displacement pump, centrifugal pump, screw compressor, etc. Relatively light load at startup.
#4 How is the customer starting, stopping and controlling the speed of the drive?
- From the keypad built into the drive, or from a remotely mounted drive keypad / control pad?
- Signals or dry contact closures feeding into the drive input screw terminals of the drive. This can come from a remotely mounted push button box with start/stop buttons or from a PLC or controller of some sort in a more sophisticated system. The most common types of control signals in this category are 24vdc PNP (+ or sourcing), NPN (- or sinking), or dry contact. An analog signal is commonly used for speed setting as well, typically 0-10 volts, or 4-20mA.
- Communication protocols such as: Ethernet-IP, Modbus RTU, Modbus TCP, Profibus, CANopen, DeviceNet, EtherCAT, BACnet (typically for HVAC)
#5 Power Requirements:
- Input voltage and phase count feeding into the drive, such as: 120VAC single phase, 230VAC single phase, 230VAC 3-phase, 460/480VAC 3-phase
- Output voltage: 230VAC 3-phase, 460/480VAC 3-phase
- Normal Duty output amperage (typically matched to the FULL LOAD AMP (FLA) rating on the motor nameplate. (Nameplate Examples) The application should be taken into account when matching a drive to the FLA rating of the drive. For example, if the motor FLA rating is 50 amps and is driving a conveyor then you would want to make sure that the drive has a HEAVY DUTY/CONSTANT TORQUE amp rating meeting or exceeding 50 amps.
#6 Does the drive need to accept encoder feedback?
This is typically used in applications where the motor has an encoder installed and provides pulse feedback to the drive for applications that require more precise speed regulation.
#7 Are there any unique special features required of the drive that may not be “standard” to most drives? Features such as advanced timer functions, customized PLC functionality to perform a specific task, motor sequencing (time shared motor operation for multiple pump systems, etc.), high Speed RPM operation greater than 400hz such as a CNC router spindle, shaft synchronization across 2 or more drives (a.k.a. electronic gearing), etc.
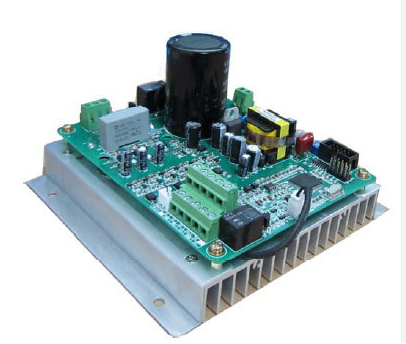
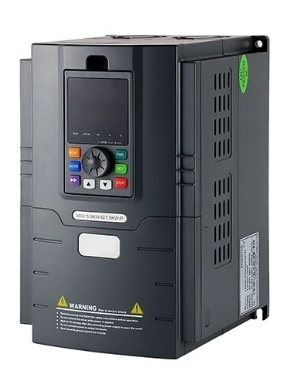
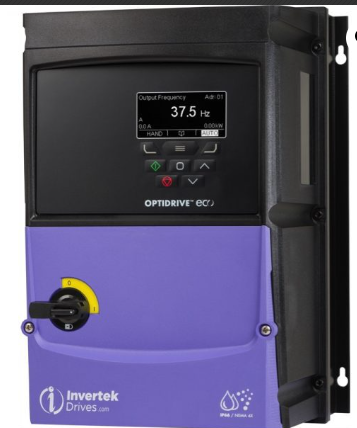